+ why "in office"?
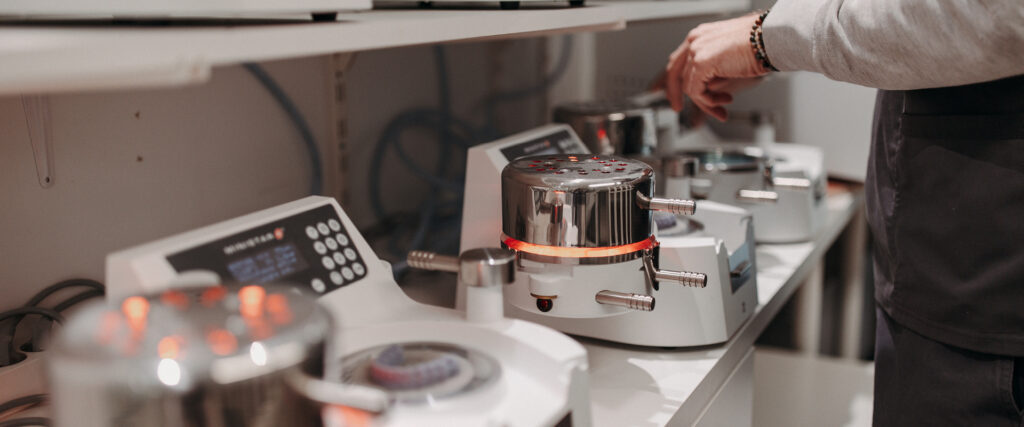
Designing and manufacturing clear aligners in-house gives us total freedom of action!
Laurent Wajdenbaum
# IN office
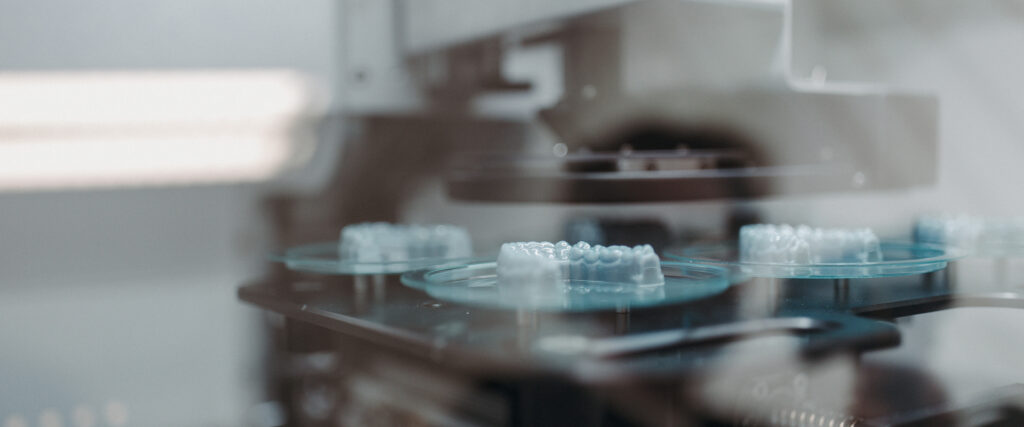
our production laboratory for orthodontic aligners
Our "ORTAL" orthodontic laboratory is a place of innovation and precision, where we work passionately to create high-quality transparent aligners. In a modern environment equipped with the latest technology, this laboratory is the heart of the manufacturing process for these revolutionary orthodontic appliances.
# Only advantages!
deadlines
flexibility
ecology
+ shorter lead times
As in many industries, the question of production lead times is crucial to guaranteeing the best possible service to our patients. Our strategy for reducing lead times is to produce some of our aligners in-house. By avoiding external suppliers, we can save precious time.
This strategy enables us to treat simple cases, recurrences and patients who have already undergone treatment in our practice. By producing in-house, the teams can work closely together, facilitating communication and coordination.
We can scan the patient's teeth in the morning and, if necessary, design, print and manufacture the aligners in the afternoon. Our turnaround times are excellent.
+ greater flexibility
Thanks to the advanced technology used in the manufacture of these aligners, they can be customized to the specific needs of each patient. This means that each mouthpiece is designed to adapt perfectly to the patient's mouth, ensuring optimum comfort throughout orthodontic treatment.
Our ability to adapt more easily is another major advantage of this laboratory. Thanks to the digital technology used in their manufacture, it's possible to make precise adjustments quickly when needed. This means that patients can benefit from more effective treatment and avoid the delays often associated with multiple exchanges with a production company outside the practice.
+ a greener approach
Producing materials in-house offers a number of ecological advantages, in particular by limiting the carbon footprint associated with transport. By producing locally, we significantly reduce the CO2 emissions generated by transporting goods over long distances.
What's more, by producing in-house, we can implement sustainable practices such as using recycled materials and reducing waste. This reduces the overall environmental impact of material production. By adopting this approach, Orthobello contributes to the preservation of the environment.